Automatic rebar bender and cutter machines, including CNC rebar bending machines and rebar stirrup bending machines, are essential tools in the construction industry. To ensure the longevity and optimal performance of these machines, regular maintenance is crucial. This article provides a comprehensive guide on how to effectively maintain your rebar bender and cutter, highlighting key aspects that contribute to machine durability and reliability.
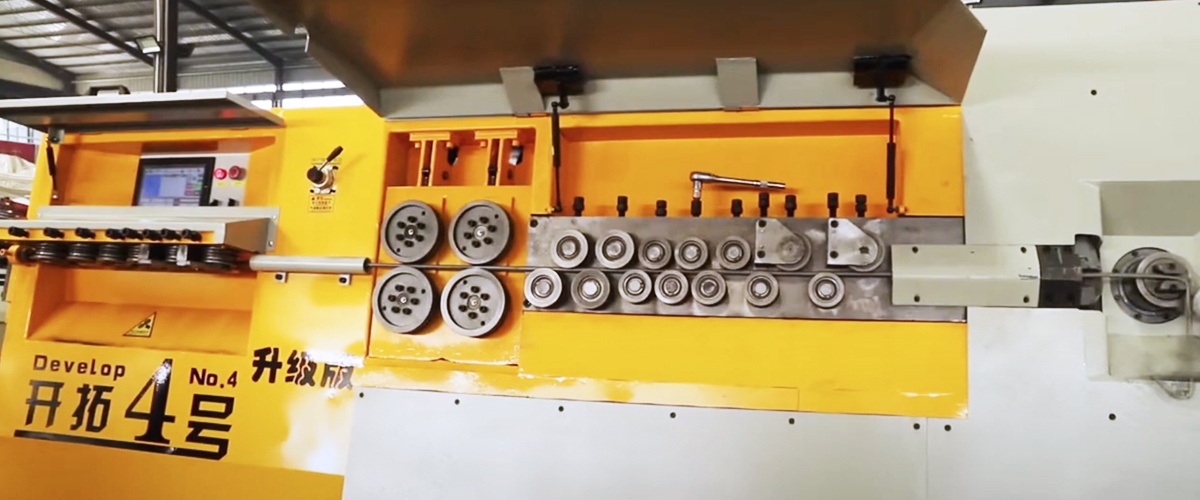
Routine Inspection:
Regular visual inspections of the rebar bender and cutter are essential for identifying potential issues early on. Check for any signs of wear, loose components, or irregularities in the machine’s operation. Addressing minor problems promptly can prevent them from escalating into more significant issues that may disrupt workflow.
Lubrication:
Proper lubrication is vital for the smooth operation of the machine’s moving parts. Regularly lubricate components such as gears, bearings, and cutting blades using the recommended lubricants. Ensure that the lubrication schedule aligns with the manufacturer’s guidelines to maintain optimal performance and reduce friction-related wear and tear.
Cleaning and Debris Removal:
Construction sites can be harsh environments, and dust and debris can accumulate on the rebar bender and cutter over time. Clean the machine regularly, removing any dirt or debris that may interfere with its functioning. Pay special attention to the cutting blades and bending mechanisms, ensuring they remain free from obstructions.
Calibration Checks:
Precision is critical in rebar processing, especially with CNC rebar bending machines. Periodically check and recalibrate the machine to ensure accurate bending and cutting. Misalignments or inaccuracies can lead to subpar results and compromise the structural integrity of reinforced concrete.
Electrical System Inspection:
For CNC rebar bending machines, a thorough inspection of the electrical components is essential. Check for loose connections, damaged wiring, or signs of overheating. Ensure that the electrical system meets safety standards and replace any faulty components promptly.
Blade Maintenance:
The cutting blades are a crucial component of rebar bender and cutter machines. Inspect the blades regularly for signs of wear and tear, and sharpen or replace them as needed. Dull or damaged blades can result in uneven cuts and negatively impact the overall quality of the rebar.
Software Updates (For CNC Machines):
If your rebar bender is equipped with CNC technology, staying updated with the latest software versions is crucial. Manufacturers often release updates to improve machine performance, enhance features, and address any potential bugs. Regularly check for and install software updates as recommended by the manufacturer.
Operator Training:
Properly trained operators contribute significantly to the effective maintenance of rebar bender and cutter machines. Ensure that operators are familiar with the machine’s operation, maintenance procedures, and safety protocols. Periodic refresher training sessions can help reinforce best practices and ensure safe and efficient use.
Conclusion:
Regular maintenance of automatic rebar bender and cutter machines is essential to prolong their lifespan, maximize efficiency, and ensure the safety of construction operations. By implementing a proactive maintenance routine that includes routine inspections, lubrication, cleaning, calibration checks, electrical system inspections, blade maintenance, software updates, and operator training, construction professionals can optimize the performance of their rebar processing equipment, contributing to the success of their projects.